Wer sind wir
Wesseling BV has been making medical aids for almost 60 years. Treatment tables, plaster table, gynecological tables, echo tables and examination tables. In addition, treatment tables and trim tables are also made for the veterinary range. But how has it all started and how is it that we do what we do now? To find out, we go back to 1958.
Henk and Truus Wesseling, living at the Houtrakkerweg 13 in Halfweg, make kitchen tables and kitchen chairs. Because this is done at home, the metalworking is usually carried out in front of the house. If one day a Physiotherapy student passes by and asks if it is possible that Henk makes a table with which he can work, the first seed is planted. He indicates that there are no proper treatment tables for his branche.
Henk Wesseling makes a table that fully matches the wishes of the client and thus the first Wesseling table is a fact. When the physiotherapist has finished his education, he decides not only to become a physiotherapist, but also as a seller of treatment and examination tables.

Expansion to the European market

Until the early 70s, the products are only brought onto the Dutch market. This changed when, in 1974, the export to Belgium was started cautiously. Now that the first steps have been taken, the desire to export is growing. Visiting trade fairs at that time was the only way to get in touch with other companies. Important contacts are being made and from that time we deliver in almost every European countries. Often the orders were delivered with our own truck, so that this could be combined with a customer visit. At the time, piles of documents were needed to allow the goods to cross the border, and this often took a lot of time.
The first intercontinental deliveries are a fact a few years later. Through a brochure from the embassy Wesseling BV comes into contact with a company in New Zealand whose owner happens to be Dutch. After a number of calls, the first orders are placed. The orders came in by post because the fax did not exist yet. If the post was not an option, there was called once in exceptional cases. However, there was an egg timer next to the phone to keep track of the time and thus the costs.
Physiotherapy is still in its infancy in the 1980s and there is a great need for equipment. Almost weekly new models are created and made to meet the growing demand.
Transition to a modern production environment
In order to not only meet the quality but also the quantity, the building on the Venenweg was opened in 1989. At that time a modern location with all the facilities that the growing company needs. An automatic sawing machine is purchased and also a welding robot. This allows production at a faster rate. The company has also been provided with a fax, and of course computers. As you can see, this has been a long time ago.
Also a showroom was be opened at the new location to showcase all products. Users can compare and test the wide variety of products here.

Growth continues under the third generation
In the 1990s, Wesseling BV grew into a leading company in the field of rehabilitation technology. The company is growing in the Netherlands and abroad, more and more countries are provided by the company with standard and customized products.
Since 2013, the company is managed by Han Wesseling and his two sons Bas and Daan Wesseling. With the third generation now interwoven in the company, the company is changing and growing. Both on the national and international market, the products and the company are still well received. Partly because of this, the demand for a broader range is large and the program is growing almost daily.
The combination of beautiful products, high quality, excellent service and customer orientation has brought Wesseling BV where it is now. The supply of serial production or tailoring of Dutch soil is unique in this market. This is one of the reasons why Wesseling BV will build on the ideas that have made the company exist for 60 years.
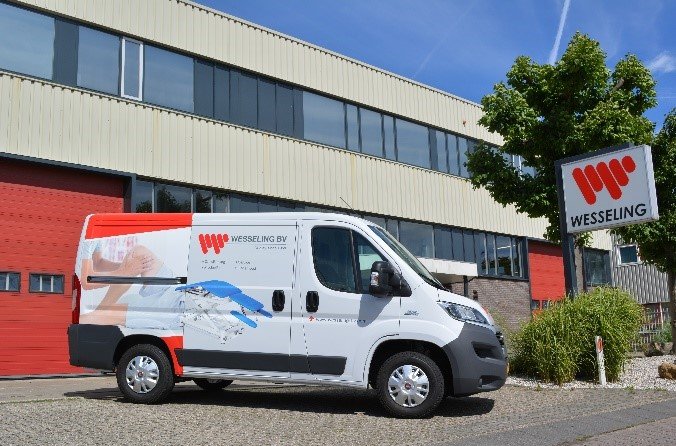
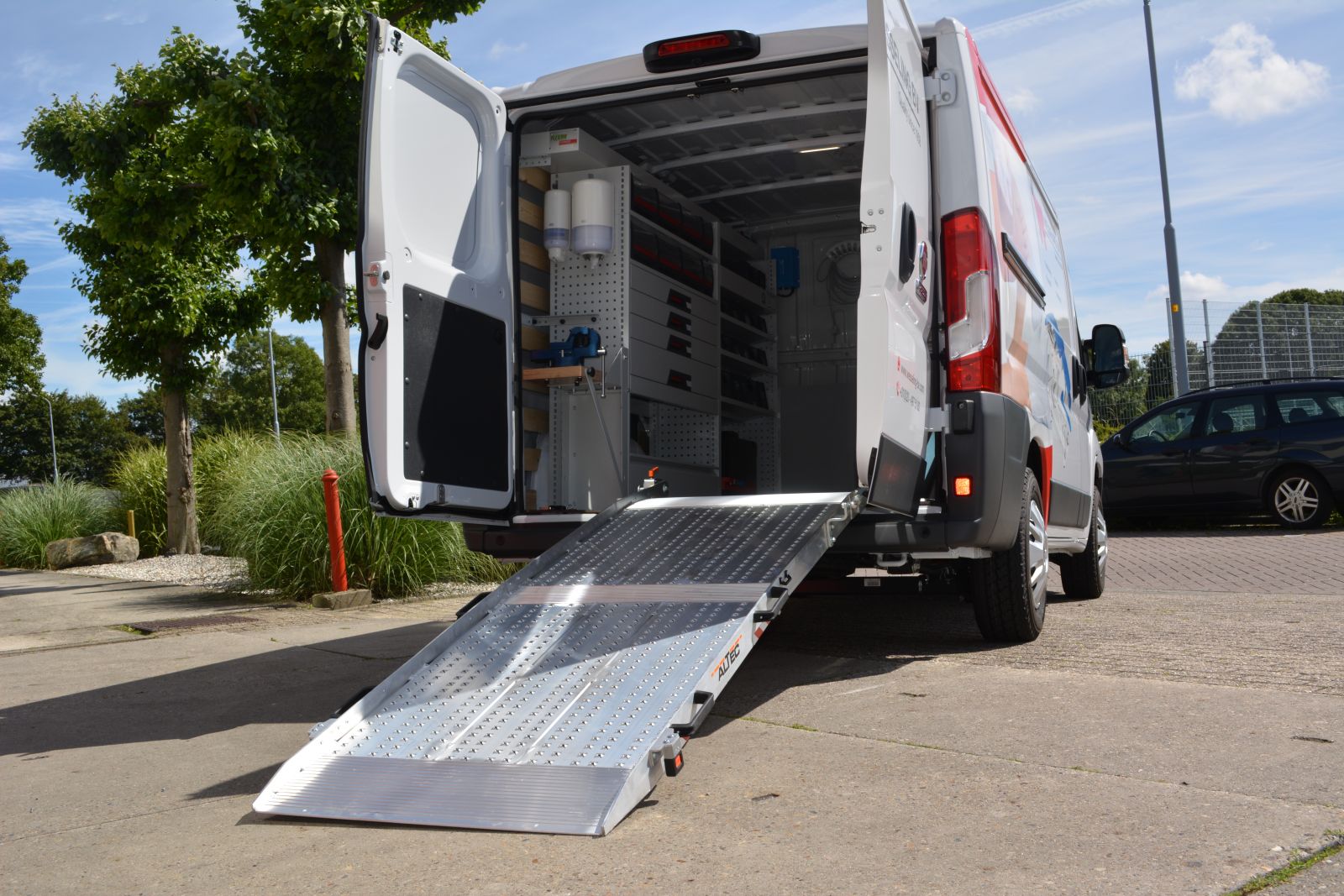
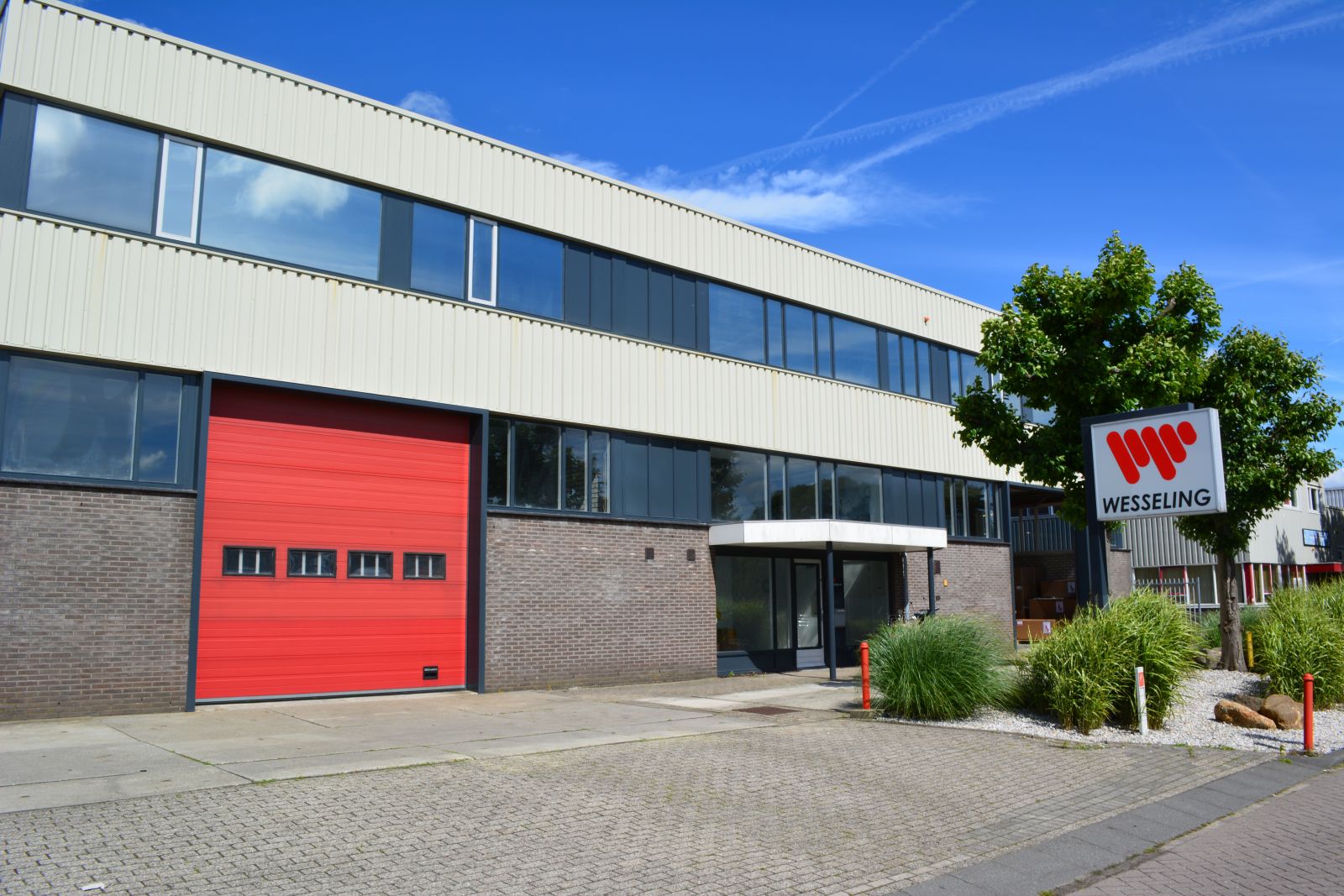
Always looking for innovations
We are constantly working on new ideas. Whether these ideas are brought forward by customers or by us, we are constantly trying to renew or improve. Some products looks the same for years, but many tables have actually been changed on small points. Stronger actuators for example, which also make less noise. Other bolts or hinge parts and other foot or hand switches. In short, changes that are not immediately visible but are certainly important for tables that meet the requirements of today.
We listen carefully to our customers and constantly try to meet their requirements. Partly because of this we have a wide choice of products that everyone can use. Our customers now know that almost everything is possible, even if it is not present in our range. So if there are any questions or comments, do not hesitate to contact us!